The United States Patent and Trademark Workplace (USPTO) has granted Nike‘s patent for a brand new footwear 3D printing course of.
Within the world style model’s novel methodology, digital designs are 3D printed onto material materials to create the shoe’s higher. The only is then 3D printed immediately onto this part, eliminating the necessity for conventional two-part shoe development methods.
Nike’s method presents superior materials customization, permitting designers to boost energy, rigidity, help, flexibility, and abrasion resistance. Eradicating heavy adhesives, stitching, and extra materials layers might additionally allow lighter footwear designs. Moreover, the newly granted patent (US-12226973-B2) has the potential to scale back materials waste, making customized merchandise extra sustainable.
David P. Jones and Ryan R. Larson are the important thing traders named within the patent, which was first filed in December 2023 and revealed final April earlier than being granted this week. Jones is a co-inventor on a number of patents associated to 3D printing immediately onto material for attire meeting. Larson, Director of Nike’s Digital & 3D Cushioning Techniques for Footwear Cushioning Improvements, can also be an energetic determine within the firm’s additive manufacturing efforts.
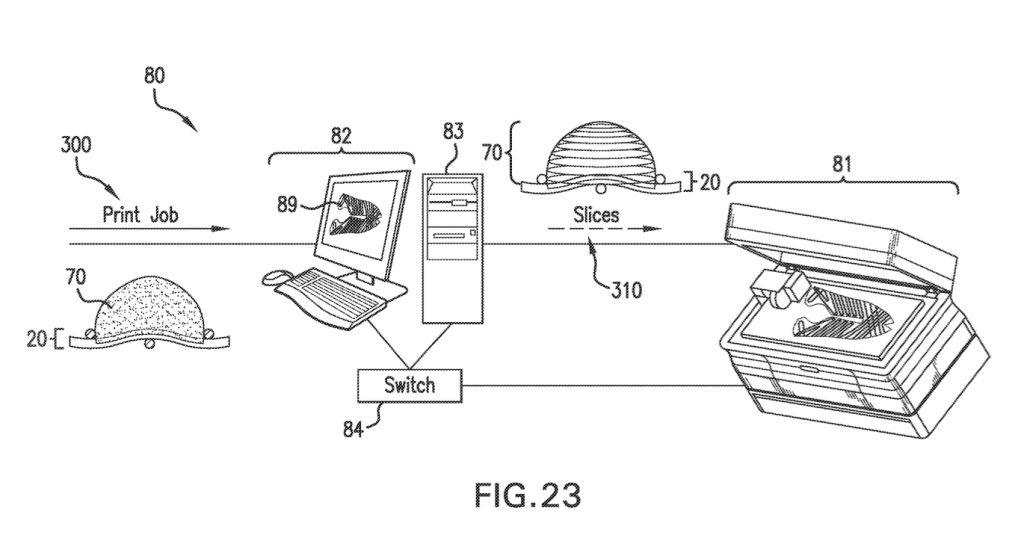
Over a decade of 3D printed footwear innovation at Nike
Additive manufacturing is nothing new at Nike. Again in 2013, the Oregon-based shoe-making big unveiled its first 3D printed soccer boot, the Vapor Laser Talon. SLS additive manufacturing was used to provide the cleat’s footplate, reportedly reducing the burden to 158 grams for sooner sprinting and optimum traction.
A number of bulletins adopted, together with a 2016 partnership to leverage HP’s Multi Jet Fusion (MJF) 3D printing expertise. That very same 12 months, Nike launched Zoom Superfly Flyknit trainers, designed for 7-time Olympic gold medal-winning sprinter Allyson Felix. Spike plate prototypes had been 3D printed in SLS to find out the right ratio of flexibility to bounce. This reportedly diminished iteration instances to days, accelerating the design course of. Legendary Jamaican Girls’s 100m sprinter Shelly-Ann Fraser-Pryce additionally collaborated with Nike to prototype customized 3D printed footwear for the 2016 Olympic Video games.
The world-leading shoemaker continued its 3D printing-enabled athlete collaborations in 2018, when former males’s marathon world-record holder Eliud Kipchoge adopted Nike sneakers with a totally 3D printed higher part.
The Vaporfly Elite “Flyprint” sneakers marked a definite transfer away from the corporate’s use of additive manufacturing, shifting from prototyping to manufacturing. On the time, Nike’s senior director for world operating footwear, Bret Schoolmeester, informed Wired, “That is the primary [3D printed] higher that will probably be extra mass relevant.” Later that 12 months, Nike prolonged the discharge of those athlete-grade trainers into the broader market.
Extra just lately, Nike made headlines final 12 months with the launch of Air Max 1000, its first sneaker produced nearly totally with 3D printing. Unveiled at ComplexCon in Las Vegas, the brand new design was developed with Berlin-based Zellerfeld, an organization identified for its 3D printed footwear experience. 1,000 pairs had been made out there by a raffle preorder on the Vegas-based style and music occasion.
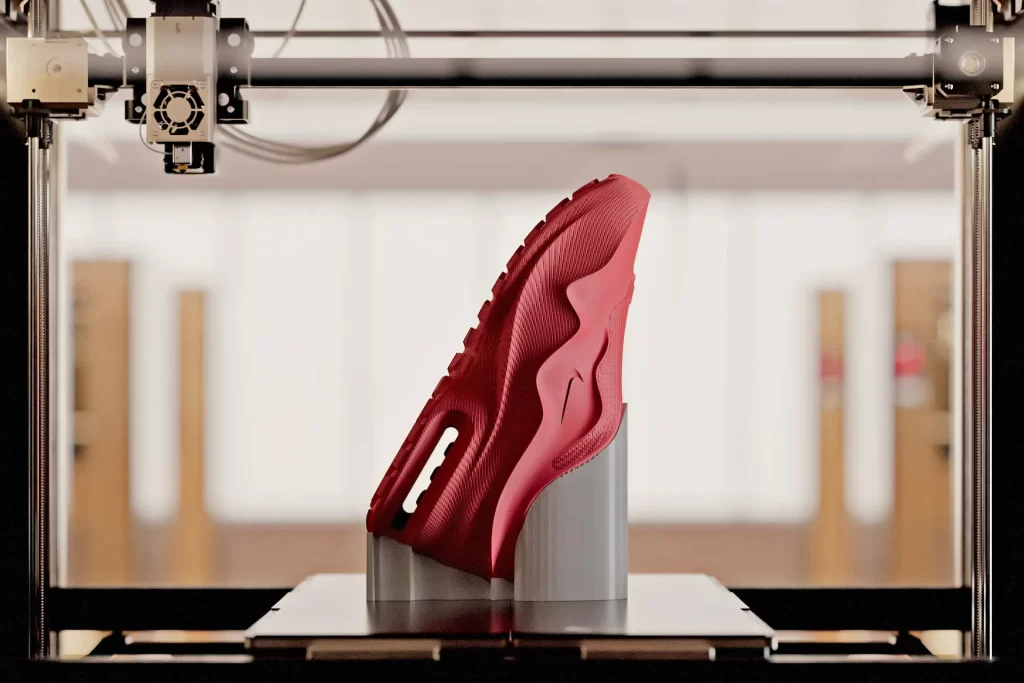
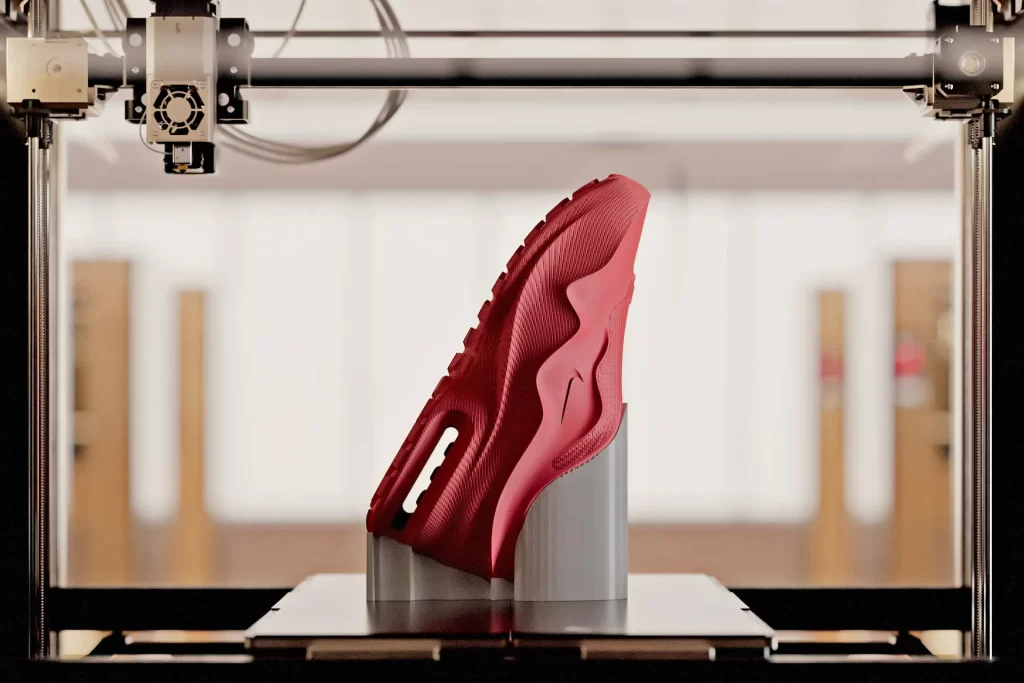
Nike’s new footwear 3D printing patent
Persevering with Nike’s additive manufacturing efforts, the corporate’s newly patented method may very well be used to manufacture 3D printed sneakers sooner or later. Based on the official doc, digital 3D patterns are first created for the shoe’s higher and sole sections. Subsequent, a chunk of knitted, woven, or nonwoven material is positioned flat on a tray inside a 3D printer. An ink, resin, acrylic, polymer, or thermoplastic-based materials is extruded immediately onto the material to create the specified sample.
Based on the patent, the extruded materials could also be barely absorbed into the material earlier than curing. Moreover, a number of layers might be 3D printed to create bolstered zones the place wanted, unlocking added energy and suppleness. As soon as printed, the sample is cured with UV mild. This step is significant to creating a robust mix between the material and extruded materials. The flat higher part is then shaped right into a 3D form, conforming to the ultimate shoe design.
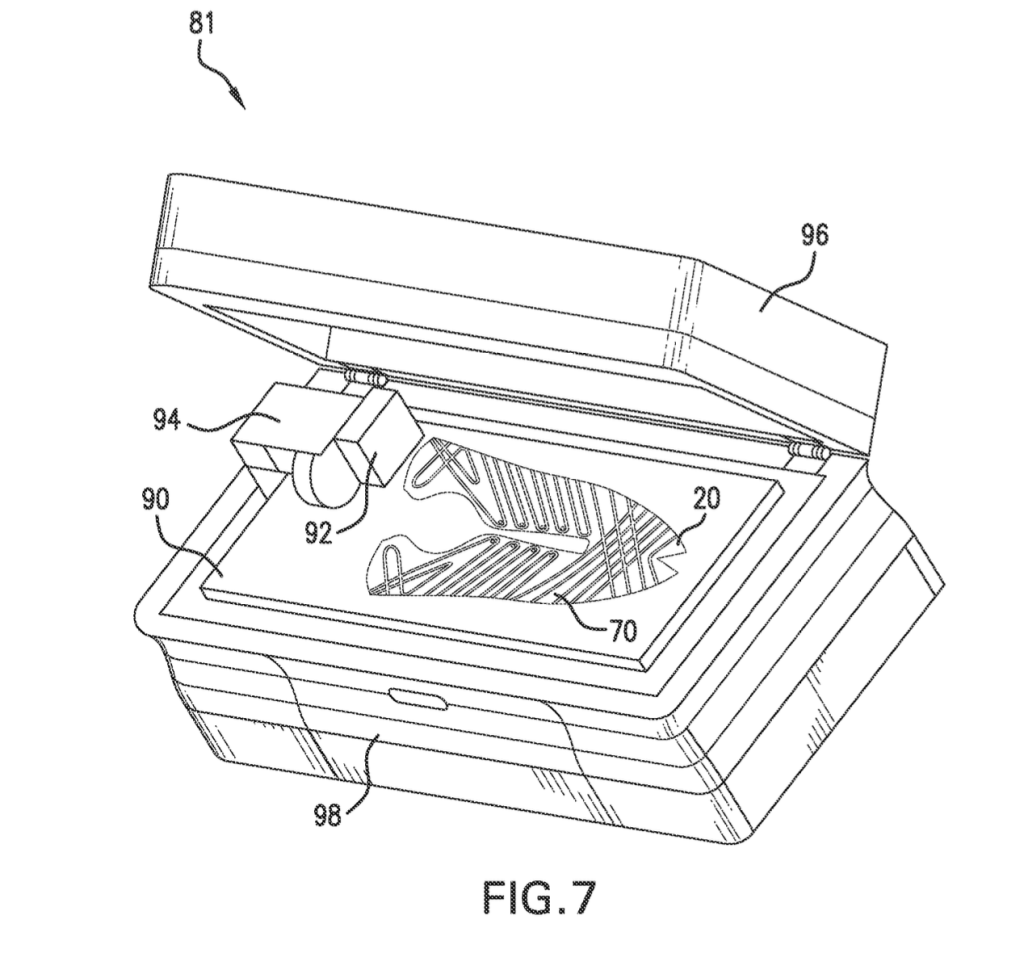
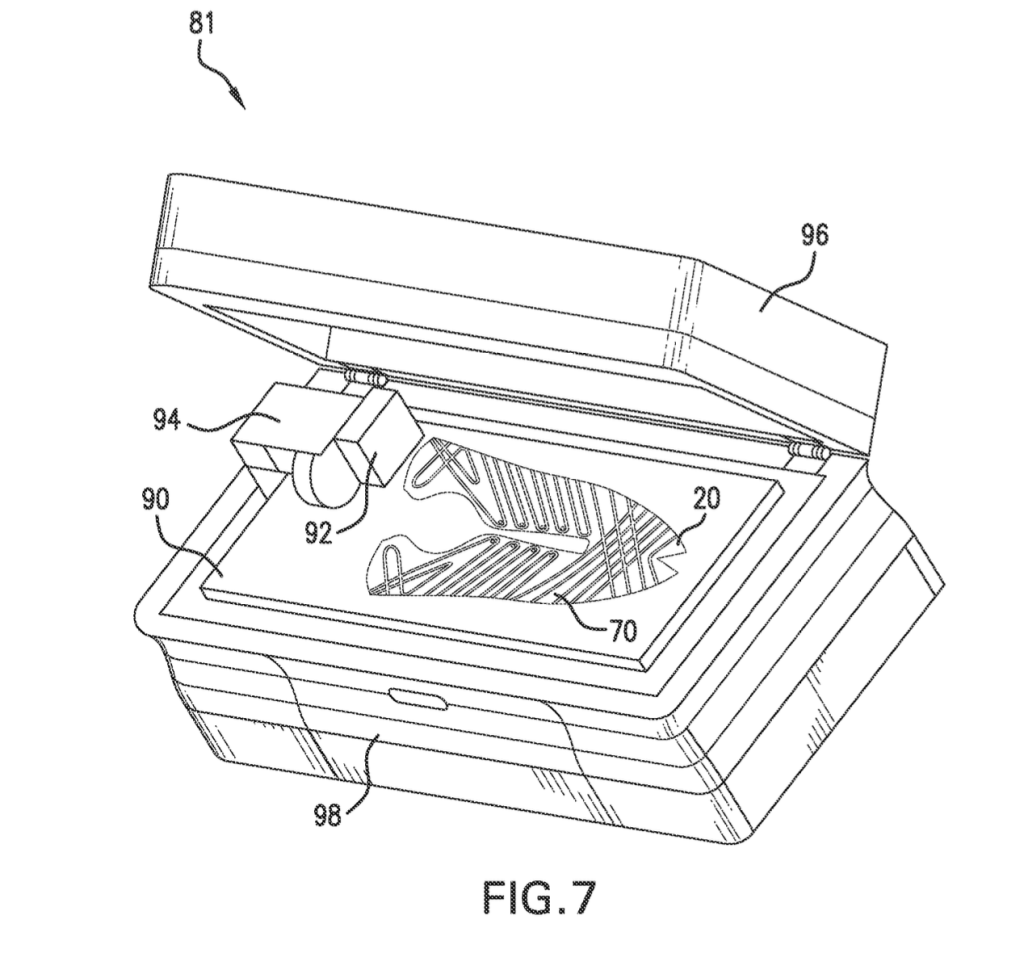
Subsequent, the higher part is positioned the wrong way up contained in the 3D printer. Utilizing at the least one pre-determined three-dimensional grip sample, the only real is 3D printed immediately onto the higher. The patent highlights that midsole and outsole layers might be constituted of versatile, cushioned supplies like polyurethane or foam rubber, enhancing consolation and sturdiness. Moreover, an non-obligatory sock liner might be added to the higher for a safer match. The only part can also be UV-cured to harden the fabric. Lastly, the finished shoe undergoes high quality management checks.
The patent signifies that this course of applies to quite a lot of sports activities footwear, together with sneakers for athletics, basketball, soccer, biking, tennis, baseball, cross-training, and mountaineering. It additionally highlights that the strategy might be utilized to create different sorts of footwear, akin to costume sneakers, loafers, sandals, slippers, boat sneakers, and work boots.
Moreover, the doc reveals that Nike’s new 3D printing course of isn’t restricted to footwear. It can be used to fabricate a spread of clothes, attire, and tools, akin to hats, jackets, shirts, gloves, and different sports activities gear constituted of material, leather-based, rubber, and foam.
This attracts parallels with different applied sciences within the garment 3D printing area. Israel-based 3D printer producer Stratasys, as an example, presents the J850 TechStyle style 3D printer. This method options direct-to-textile expertise that may 3D print designs and patterns immediately onto clothes akin to denims and jackets. The 3D printer is appropriate with denim, cotton, polyester, and linen materials, permitting designers and style manufacturers to personalize wearable merchandise and meet buyer model preferences. Based on Stratasys, its style printing course of minimizes materials waste by changing outdated outfits into new, bespoke style merchandise.
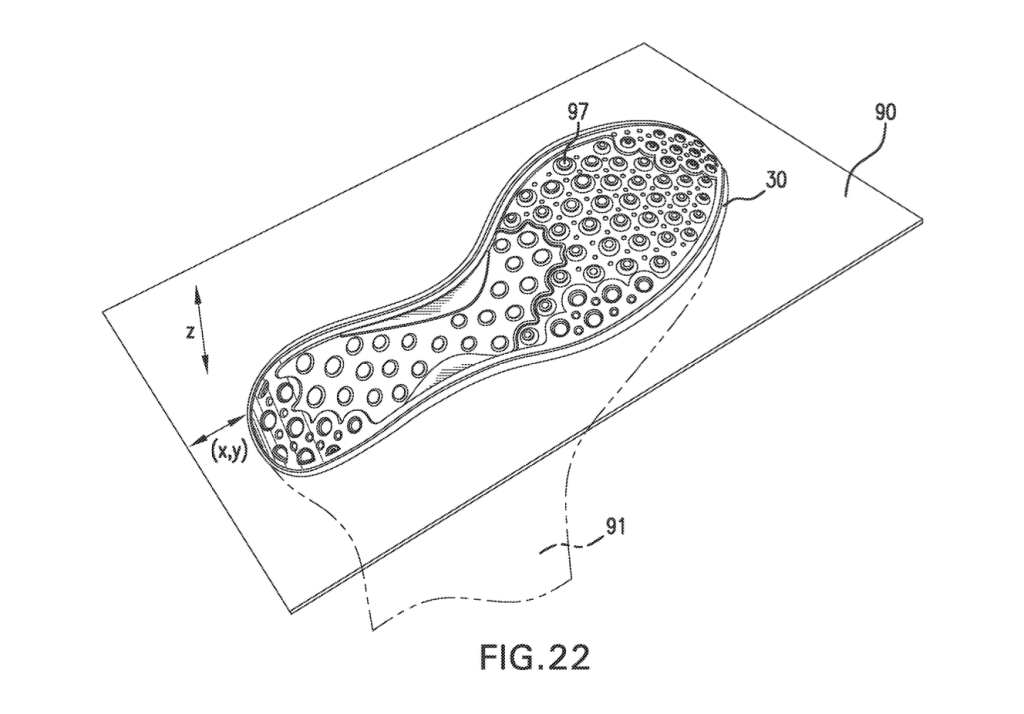
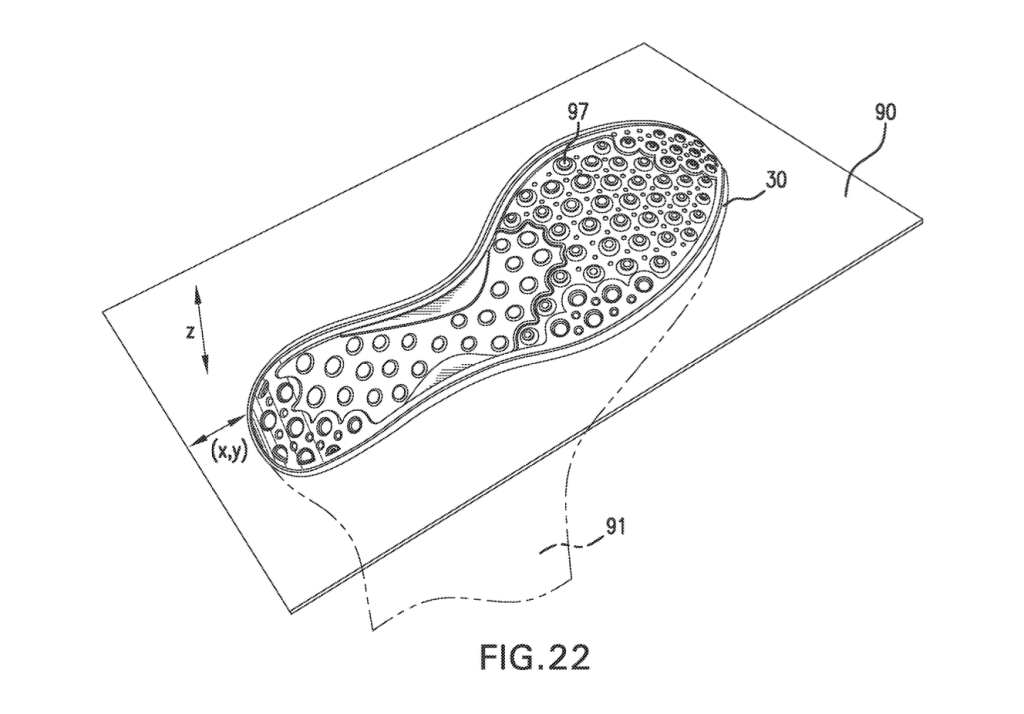
3D printed sneakers: a rising trade pattern
3D printed sneakers are a rising pattern within the additive manufacturing and footwear industries. Rising curiosity is pushed by the expertise’s potential to create distinctive and customized designs to satisfy buyer wants with minimal materials utilization.
Nike isn’t the one footwear model to embrace additive manufacturing. Earlier this 12 months, the posh Italian style model Gucci expanded its Spring Summer season 2025 (SS25) assortment by introducing a number of new designs of its 3D printed Cub3d sneakers. Initially launched final 12 months in a restricted run of simply 20 pairs, the sneakers at the moment are out there in 5 colour choices: Purple, Gray, Black, Brown, and Gray-and-white.
These 3D printed sneakers mix Demetra and mesh of their higher development. Gucci developed the Demetra materials, at the least 70% of which consists of vegetable-derived uncooked substances like viscose, wooden pulp, and bio-based polyurethane. The bi-material sole options an EVA-filled cushioning inside and a TPU exterior for added flexibility.
Elsewhere, Florida-based footwear developer Syntilay just lately launched new 3D printed sliders designed utilizing synthetic intelligence (AI). Out there for $150, the sneakers are 3D printed to satisfy particular buyer specs. Patrons scan their toes with a smartphone digital camera to provide an correct mannequin for sizing. Human designers sketch the preliminary ideas earlier than AI platforms like MidJourney refine these concepts into extra detailed types. AI design software program Vizcom then converts the sketches into 3D fashions, that are fabricated in collaboration with Zellerfeld.
One other firm 3D printing footwear is ELASTIUM. Final 12 months, the UAE-based startup partnered with LaLaLand Manufacturing & Design, California’s largest shoe producer, to broaden additive manufacturing within the footwear trade. The businesses are working to speed up localized and sustainable mass manufacturing by their No-MMOQ hybrid manufacturing mannequin, which may reportedly minimize preliminary funding prices by as much as 80%.
The primary product launched underneath this collaboration, the Orca, Elastium’s newest 3D printed sneaker. It combines a TPU foam midsole with an elastane and TPU higher. Delivery for this product commenced final November, with costs beginning at $250.
Who gained the 2024 3D Printing Business Awards?
Subscribe to the 3D Printing Business publication to maintain up with the newest 3D printing information.
You can too comply with us on LinkedIn, and subscribe to the 3D Printing Business Youtube channel to entry extra unique content material.
Featured picture exhibits schematics of a Nike shoe. Picture through america Patent and Trademark Workplace.